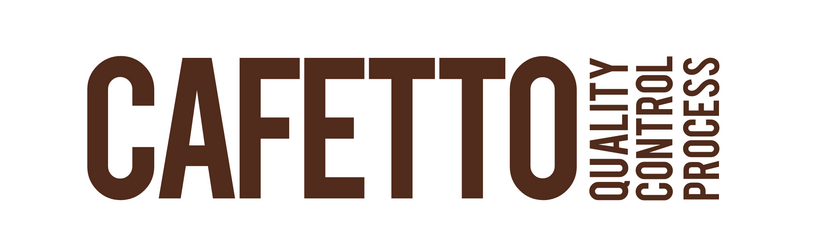
The best way to think about Quality Control (QC) is as one of the most pivotal functions in Operations where product integrity and compliance meet. This is essentially the stage where products and processes are placed under the microscope to judge whether they're up to Cafetto's internal standards for commercialisation.
The measures put in place for assurance of QC have an on-flow effect to all other departments within the Cafetto business, as it's the first point of call for assuring the integrity of our products is met and maintained. Additionally, it's a significant component to upholding our certifications systems. Here's how it breaks down into daily operations:
A day in the life of QC 🥼
The average day begins with the QC team gathering solutions and calibrating equipment, ready to test finished product samples.
The sample undergoes testing following a series of QC protocols. Once passing, the results are obtained. It is then released to Production who prepare it for the next step: getting the product to pressing and packing. Every batch of Cafetto products is then certified with the Certificate of Analysis (CoFA).
The CoFA is designed to assure the customer the product is compliant with the quality, performance, and safety standards for market.
This is then followed by collecting a sample of the completed batch, also known as a retention sample. This is something we at Cafetto are required to do for both quality assurance and retesting purposes for each Cafetto product.
Each of these are prerequisites for the creation of the Quality Control Record. This is an essential piece of documentation that holds us accountable, ensuring manufacturing processes are meeting the standards required for each Cafetto product.
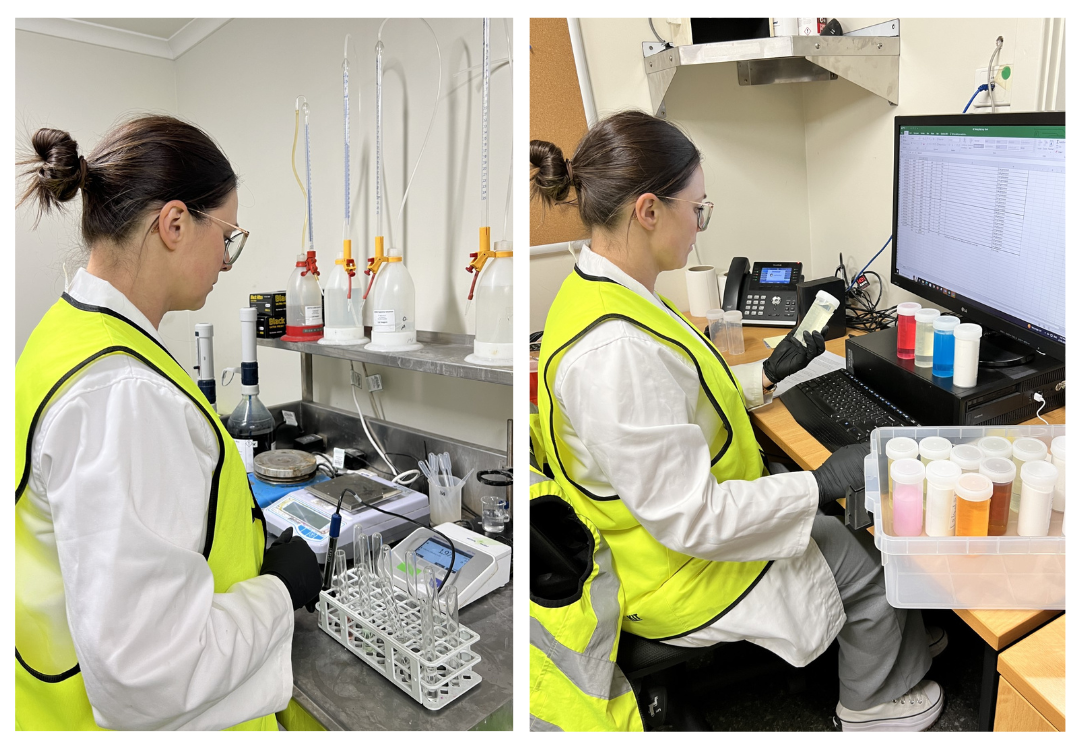
How do these processes contribute to the big picture?
In conjunction with these steps, the QC team is responsible for overseeing various reporting databases throughout the business. A few of which include:
Environmental Monitoring 🧑🏼🔬
This is where samples at selected points throughout the Cafetto manufacturing area are collected to test microbial activity/levels.
This is a good example of Quality Control diligence that flow-on to various business sectors, as environmental monitoring is a core requirement to maintaining our ISO 22000:2018 Food Safety Management / HAACP (Good Manufacturing Practice) Certification.
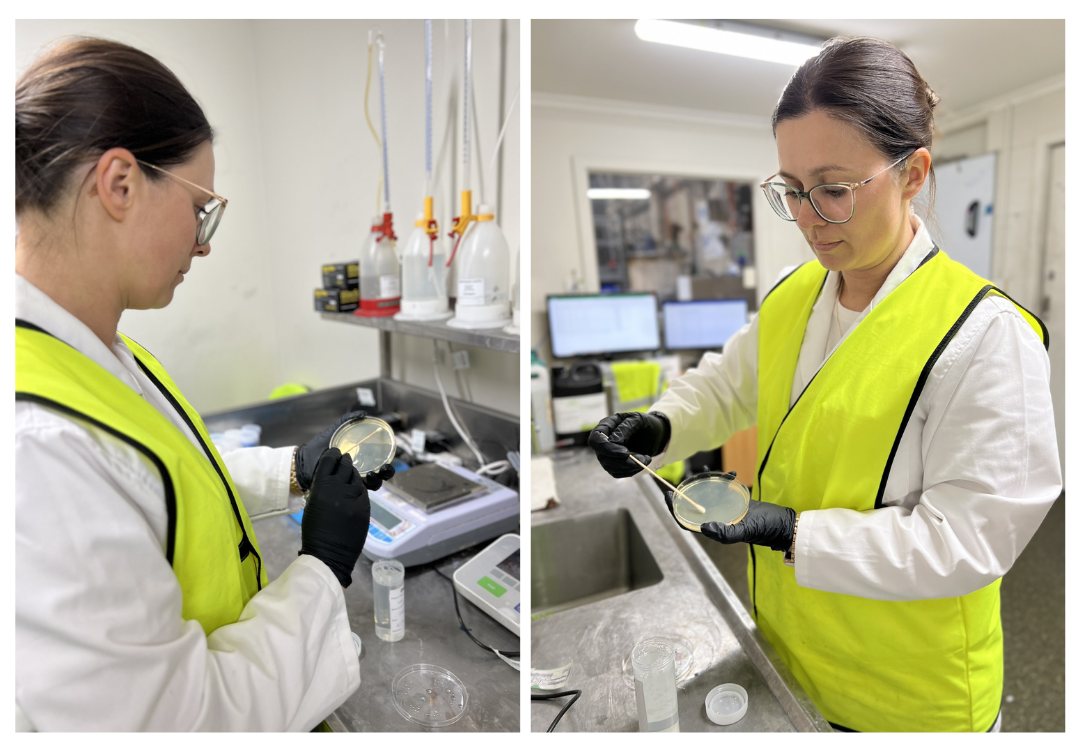
Approved Supplier Program
As part of our Quality ISO 9001 Certification, Cafetto implement an Approved Supplier Program system, which assesses our critical suppliers to ensure we’re using quality raw materials from reputable sources for Cafetto products. This is crucial to upholding our commitment to providing each customer with reliable, high-quality products they can trust.
As of such, a pivotal step in Quality Assurance Management is the assessment of technical documentation for each raw material that is used in Cafetto products. This is essential to answering the following:
- Do the raw materials meet our internal specifications?
- Do they align with the standard of quality and safety we want to provide our customers?
The tableting process 💊
With each step in quality control, there’s an extra set of precautionary testing that takes place to satisfy complete quality assurance. Our tableting process is a great example of this, as each batch is put through rigorous testing before manufacture. Here’s a snapshot of what the tableting testing during the product filling process looks like:
Weight & Dimensions ⚖️
Before the tablet process begins, it is important to check the tablet set up process produces tablets that are within the weight and dimensions outlined in the product's specifications.
Hardness Check ✅
Tablets are then placed into callipers to test whether they meet the conditions for hardness specification.
Friability Check ✔️
Also known as the crumble check, tablets are placed into the friability tester to check how well the tablet keeps its shape after several minutes.
Dissolution Test 💧
The last step is to closely monitor how long it takes for the tablets to completely dissolve, (average dissolution time varies per tablet size), to replicate the usage instructions of the product specification.
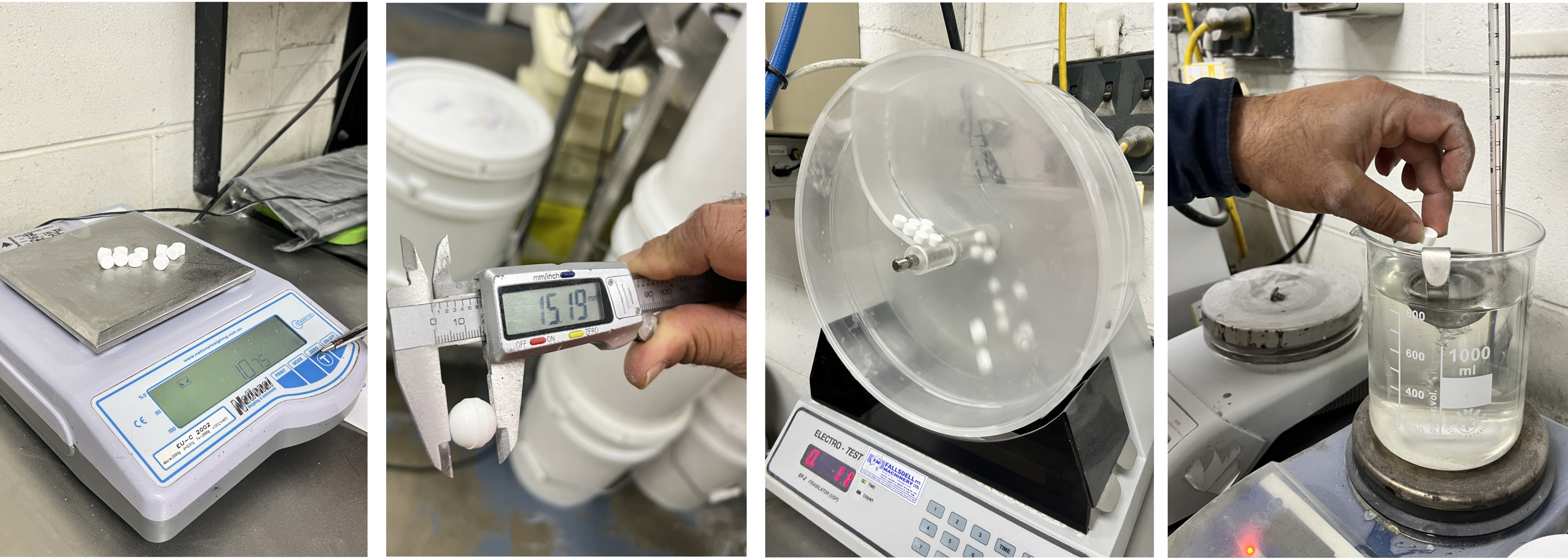
This information is required during various stages of the tableting process which includes first off check, regular intervals during the tableting process, and last off checks. Other information requested also includes environmental data.
The finishing process
Only after the testing reports are well documented can the products be filled into jars.
Our tablets are placed onto the filling counter, where the machine is set to dispense the correct amount of tablets required for each product variation size. The jars are filled in a way that protects the product from damage and absorbing any moisture. This helps to maximise the product efficacy and quality.
Once the tablets are filed into jars, they’re securely sealed with a tamper evident cap, labelled with a batch number, manufacturing dater and expiry date.
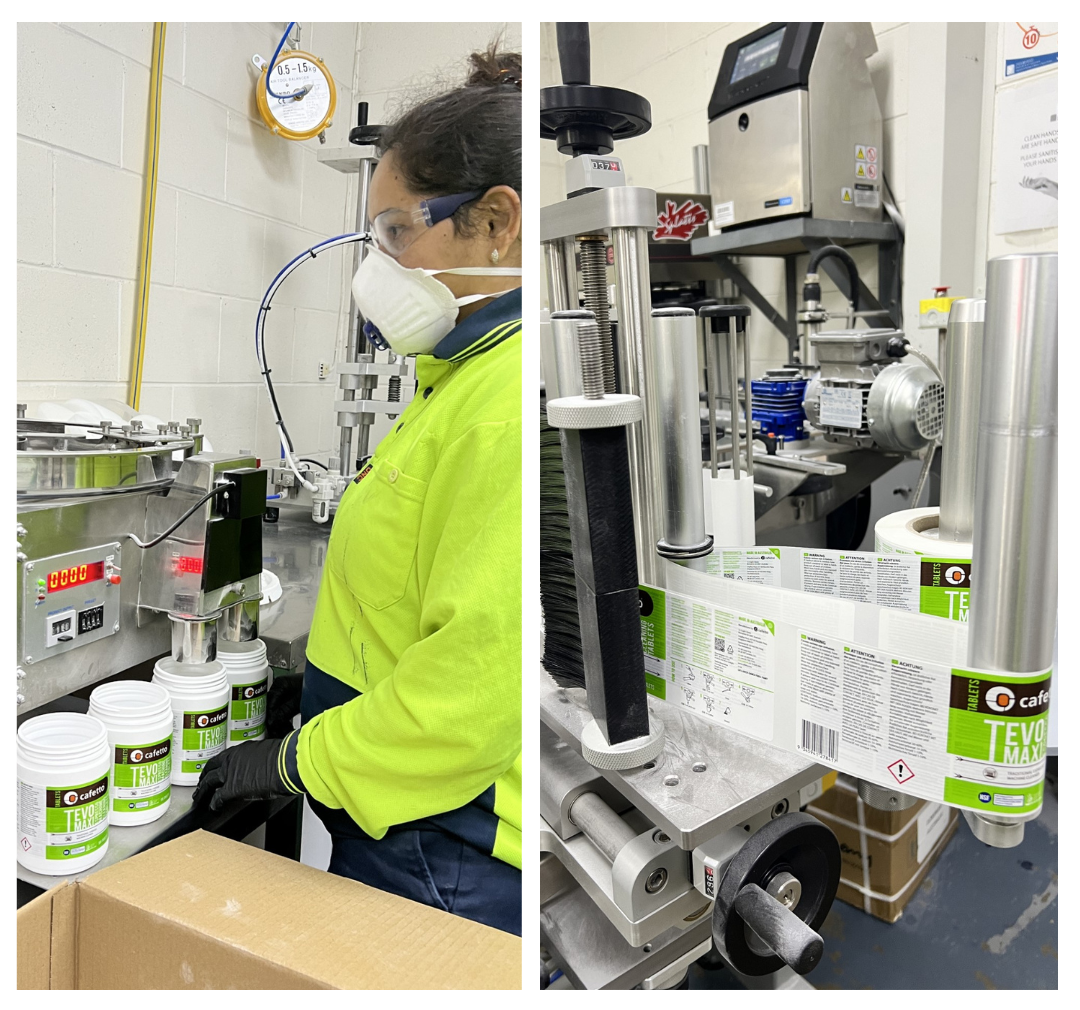
QC’s responsibility to relay the key information to relevant departments is a fundamental part of our commitment to continuous development and ensuring complete transparency across various business functions.
From idea to final product, Quality Control plays an important role with all processes we at Cafetto have in place. To learn more about what we to do protect our consumers, click here.